Ever wondered about the production process behind Hans J. Wegner’s iconic CH24 Wishbone Chair?


The Wishbone Chair, designed in 1949, was part of the first collaboration between Hans J. Wegner and Carl Hansen & Søn and it has been in continuous production ever since. By combining the top rails and arms into a single piece, Wegner took a giant leap in furniture design with this piece. To give stability to the steam-bent top and ensure comfortable support, he developed the characteristic Y-shaped back that earned the chair its famous name. The woven paper cord seat was originally chosen as a substitute after WW2 when materials were in short supply, but Wegner grew to appreciate paper cord for its strength, design qualities, and natural look and feel. Wegner had an impressive career, with more than 500 chairs in his portfolio, but his Wishbone Chair holds a special place in the design world and has achieved iconic status worldwide, celebrated for its functionality and classic, timeless aesthetic.
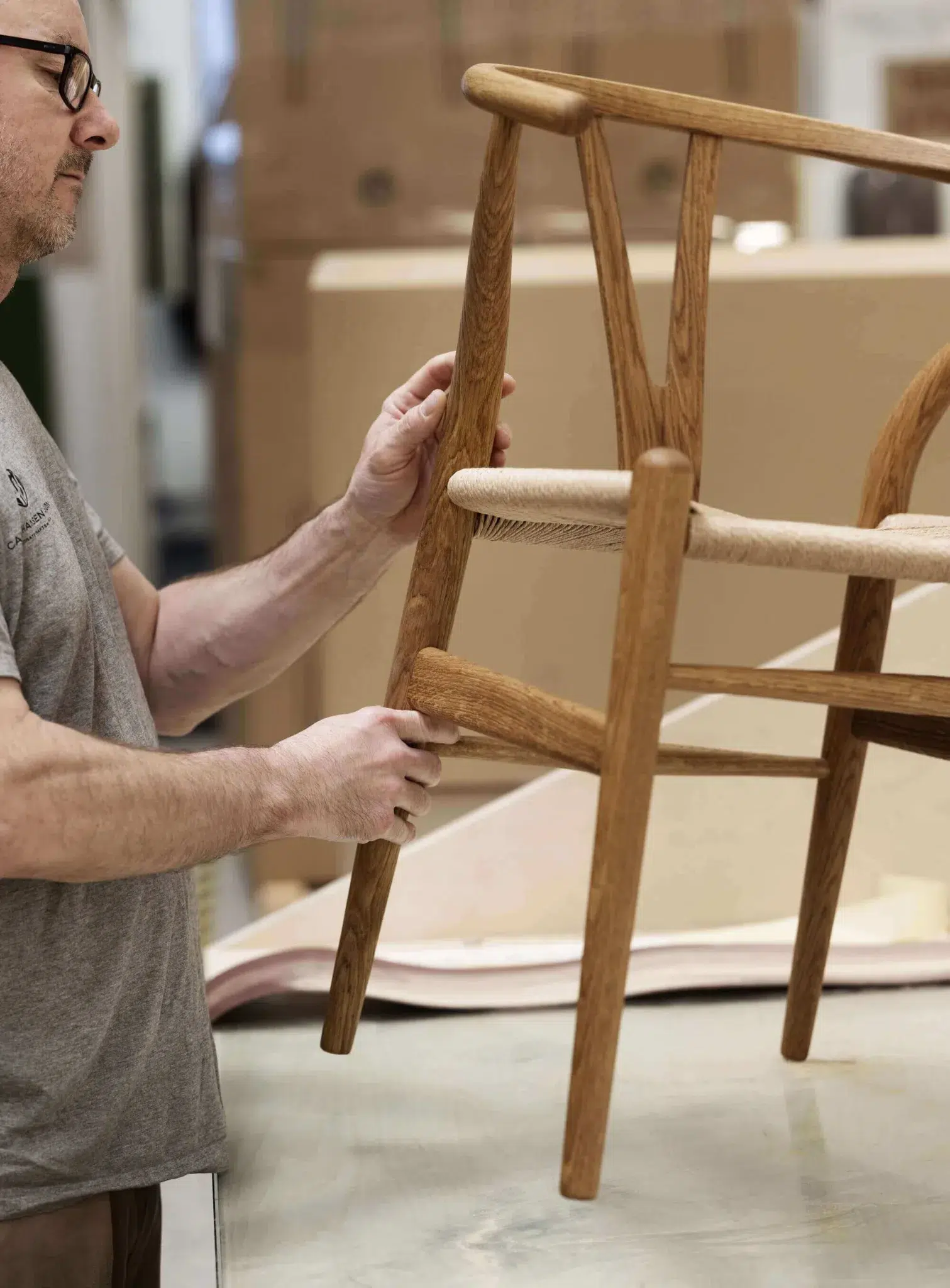
Each Wishbone Chair consists of 14 parts made in oak, beech, walnut, mahogany, ash, or teak. All wood is certified and/or from sustainable forestry. More than 100 production steps are required to assemble the Wishbone Chair, most of which are carried out by hand. Here are some of them:
- Sanding is essential to the final finish of the piece to achieve a smooth and tactile surface.
- All parts are assembled with glue by hand.
- The parts are pressed into place to ensure optimal stability, using a special compressor designed just for the Wishbone Chair.
- The frame is examined and all joints are double-checked.
- The Wishbone-part is glued into the backrest of the chair.
- The backrest and Wishbone-part are assembled onto the frame of the chair.
- The height of the chair is measured to make sure it is even and stands on all four legs. If not, the feet are sanded until the chair is completely even.
- Finalizing the assembly, a special torch is used to make sure no glue is visible. Any leftover glue is removed with a soft sponge.
To achieve a beautiful surface, additional durability, and easy cleaning, the Wishbone chair is treated with either oil, soap, lacquer, or paint.

The seat of the CH24 is hand-woven using 150 meters of paper cord. It takes an experienced weaver one hour to create the CH24’s seat.
- The seat is woven with a special envelope-woven technique. The first piece of paper cord is stapled onto the inner frame, and from there on, the seat is secured with nothing but tight weaving and special knots.
- A weaver uses 5-6 meters of paper cord at a time and ties a sheet bend knot when combining the pieces of paper cord. The knots are hidden inside the weaving.
- Once the seat is woven, a small plate of authenticity is placed underneath the seat with the chair’s unique serial number.
- A final quality check makes sure that the chair is even and lives up to the quality standards of Carl Hansen & Søn.
After being processed by eight sets of skilled hands, the Wishbone Chair is ready to leave the factory located on the Danish island of Funen.

Get insights into the traditional techniques of paper cord weaving at London Craft Week in the Carl Hansen & Søn Flagship Store London, 48A Pimlico Road, SW1W 8LP. Call 020 77308454 or visit carlhansen.com. Follow on Instagram @carlhansenandson_london and @carlhansenandson.